What are the testing items for lithium batteries?
- Share
- From
- Carol
- publisher
- Carol
- Issue Time
- Sep 26,2020
Summary
【Summary】:
In order to ensure the safety of lithium-ion batteries, domestic and foreign institutions have formulated various safety testing standards for lithium-ion batteries. General testing standards generally divide safety testing items into the following four categories:
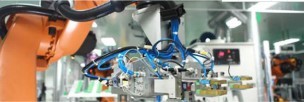
What are the testing items for lithium batteries?
【Summary】:
In order to ensure the safety of lithium-ion batteries, domestic and foreign institutions have formulated various safety testing standards for lithium-ion batteries. General testing standards generally divide safety testing items into the following four categories:
1. Electrical test: overcharge, overdischarge, external short circuit, forced discharge, etc.
2. Mechanical test: extrusion, acupuncture, shock, vibration, drop, etc.
3. Thermal test: high and low temperature cycle, combustion, microwave heating, etc.
4. Environmental simulation: high altitude and low pressure simulation, salt spray test, etc.
Extrusion, acupuncture, impact, vibration, drop, burning, high-altitude and low-pressure tests all require professional battery testing machines for testing. In order to ensure the safety performance of the battery, check for unqualified batteries and avoid battery safety accidents.
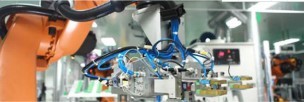
The above tests are all finished lithium battery tests, but if testing equipment can be added to the production process of lithium batteries, the qualification rate of finished batteries can be effectively improved. The structure of the battery includes shell, upper cover, pole plate, separator, bus bar, pole, bridge protection plate, terminal and other components. The production process is complicated and cannot be detected by naked eyes through outsourcing. This is X-Ray real-time imaging Technology is a good choice. X-rays are emitted through the X-ray generator and penetrate the inside of the lithium battery. The imaging system receives the X-rays and takes pictures. Then the image is processed by related software and automatically measured and judged to identify the internal defects of the lithium battery. The terminal can be docked with the production line, fully automatic loading and unloading, reducing labor costs, realizing the integrated operation of production, testing, and determining, which plays an irreplaceable role in detecting the yield of lithium batteries and improving production efficiency.
In general, lithium batteries have higher requirements for product quality and safety, product consistency, and subsequent maintenance costs. The quality of their products needs better assurance, so the detection of lithium batteries is particularly important.